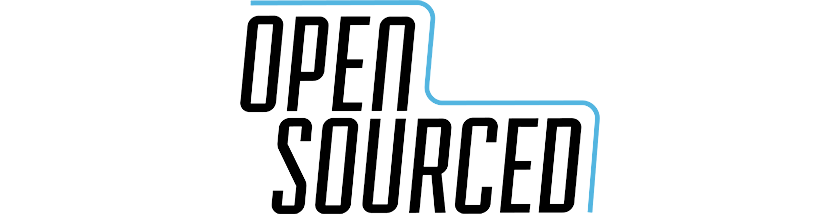
Even a year after the pandemic started wreaking havoc on global supply chains, a chip shortage is still disrupting entire industries.
This year, some of GM’s newest cars won’t have a critical feature — an advanced fuel management system that saves gas — because the company couldn’t get enough chips, the transistor-filled semiconductors that keep so many of the devices we use today running. After announcing in March that customers who buy the new Chevrolet Silverado and GMC Sierra pickups between now and the end of the summer will have a lower fuel economy, GM said Thursday that worsening supply chain issues have led to temporary closures of eight of its assembly plants, affecting about 10,000 workers.
GM isn’t the only automaker facing setbacks and even layoffs due to the shortage. In March, Ford said the chip shortage, along with weather conditions, left the company canceling shifts and building some vehicles without all their parts. Honda, Volkswagen, and Toyota have similarly warned of supply issues or reduced production in recent months.
Meanwhile, the United States has struggled to bring in enough of everything — from much-needed N95 respirators and other personal protective equipment to bicycles to game consoles and laptops — since Covid-19 first arrived. The chip shortage has continued to hurt device makers, too. Samsung recently warned that it might skip the introduction of its popular Galaxy Note phone this year. It doesn’t help that other shortages, including a shortage of shipping containers, are also causing ripple effects in the supply chain.
But the chip shortage, specifically, points to particular weaknesses in the US high-tech manufacturing industry. In response to growing concerns about the chip shortage and its consequences, President Joe Biden signed an executive order in February starting a 100-day review of supply chains for critical products, with a particular focus on advanced technology components, also fulfilling one of his campaign promises.
Biden’s review won’t just look at the US supply of semiconductors. In the coming weeks, the administration will continue to review America’s manufacturing abilities for pharmaceuticals, high-capacity batteries, and rare-earth elements that are found in everything from lasers to electric vehicles. There’s also a broader, yearlong review of sectors ranging from food and energy to transportation. The ultimate goal, the president said in February, is “making sure the United States can meet every challenge we face in the new era.”
The review could be essential to helping the US economy recover and could better prepare the country for a future crisis. Even as millions of people get vaccinated against Covid-19 and the economy picks back up, supply chain disruptions linked to the chip shortage are proving particularly persistent. The impact of the chip shortage on US autoworkers alone prompted governors from eight states to urge Biden to take action in late February, and Sens. Marco Rubio and Chris Coons have asked Biden to invoke the Defense Production Act to boost semiconductor supply.
“More than a warning, [the pandemic] was a data point for us that this can happen — and if it happens, look what it can do,” explains Seckin Ozkul, the founder and director of the Supply Chain Innovation Lab at the University of South Florida. “[When] a big disruption happens, how can you make sure that your supply chain is going to recover and not have major impacts as soon as possible?” Monday alone demonstrated how fragile the chip situation is. A fire at one automotive chipmaker’s factory in Japan sent stocks in Toyota, Nissan, and Honda down more than 3 percent.
But boosting US supplies of chips, or any other high-tech product, can’t happen overnight. Building new manufacturing facilities can be tricky, time-intensive, and expensive, and some previous government efforts to boost high-tech jobs in the US have failed. At the same time, recent decades have seen more and more of this manufacturing taking place outside the US, in part because it can be cheaper, easier, and more efficient to make these high-tech products abroad.
Now that the Biden administration has started down the difficult path of analyzing just how insecure America’s supply chain for these hard-to-manufacture components is, the companies affected by the shortage are trying to figure out what to do until a solution appears on the horizon. While this review alone won’t boost US high-tech manufacturing, the hope is to set the groundwork to secure US supply chains before another crisis hits.
Making chips is hard
When the pandemic arrived, the demand for computers and other electronics skyrocketed as many people shifted to working, learning, and playing at home. Like many other manufacturers, chip producers also had to adapt and in some cases close down their facilities due to Covid-19 safety measures. Because chip manufacturing is a long, complex process — the Semiconductor Industry Association says lead times for semiconductor orders can be as long as 26 weeks — surging demand and limited supply have caused ripple effects that the manufacturers and customers are still feeling a year later.
“Making a semiconductor is perhaps the most highly complex manufacturing process on the planet,” Falan Yinug, SIA’s director of industry statistics and economic policy, told Recode. “It can involve more than a thousand process steps and hundreds of advanced machines needed to pack tens of billions of transistors on a chip the size of a quarter.”
Then there’s the fact that only a few existing manufacturers, such as Intel and Samsung (which helps make chips for companies like Nvidia), currently have the capacity to produce these semiconductors. Complicating chip supplies even further are limits the Trump administration placed on the largest China-based chip manufacturer, SMIC, amid ongoing trade tensions. Now, without enough semiconductors to meet global demand, we’ve seen shortages in chips needed for everything from PlayStations to Ford F-150s. In April, Nikkei reported that the chip shortage was even delaying production of Apple’s MacBook.
Some automakers are facing even worse delays because of decisions they made in the pandemic. When Covid-19 first arrived, some carmakers gave up their spot in line to buy semiconductors, in anticipation that the economic downturn would reduce demand for vehicles. At the same time, device makers that saw a surge in demand for their tech rushed to pick up chip orders that would have otherwise gone to the automakers.
A year later, there’s now much greater demand for cars, and companies like GM and Honda want more chips so they can increase their production. But now, these automakers are not only competing with increased demand for chips from device manufacturers, but also facing monthslong delays for their own orders. “Fast forward, May hits, and then the automobile plants are back online, and then they start placing orders,” explained Patrick Penfield, a supply chain professor at Syracuse University. “But now you have a hole in the pipeline.”
Now, the chip shortage is holding up production lines in car and truck plants. As a result, some autoworkers are idle, and some have even been laid off. That’s only fueled concern among US politicians and some industry leaders about the US’s relatively meager domestic manufacturing capacity for these chips, and high-tech manufacturing more broadly. Senate Majority Leader Chuck Schumer recently warned, “Semiconductor manufacturing is a dangerous weak spot in our economy and in our national security.”
Just 12 percent of global chip manufacturing is now based in the US, compared to the 37 percent share that the country had in 1990, according to research SIA conducted with the Boston Consulting Group. The primary reasons for this decline are, according to UCLA supply chain professor Christopher Tang, the low cost of production in other countries and chemical processes with less stringent regulation abroad.
“We never had a coordinated plan, meaning these are free markets. So any companies can ship anything outside the country,” Tang explained. “So now is a wake-up call. We have shifted virtually everything, so now it’s an empty vault.”
There are many ideas for how to boost high-tech manufacturing in the US. Some, like Tang, say that part of the key is boosting the number of US students who study STEM and creating more high-tech jobs in the field. Another strategy up for consideration is beefing up US “industrial policy,” which would have the government take a more active role in encouraging high-tech industries in the US, whether through tax benefits, direct investment in research, or government subsidies. In his presidential campaign, Biden even proposed wielding the government’s power to buy these supplies directly from US manufacturers. Now with his supply chain review, Biden appears to be taking a first step toward pursuing that goal.
Biden wants to see how high-tech American manufacturing can be
Biden’s supply chain review is a first step toward better understanding what the weaknesses in US supply chains are, before starting the more costly process of what to do about it.
“In general, we are vulnerable to disruptions on global interconnected supply chains. What are the solutions to that?” said North Carolina State engineering professor Julie Swann. “First, understand your supply chain, right? Know where your risks are, so that you’re not caught unawares when it happens. And that requires, really, a deep dive in many different industries.”
In part, a Biden administration official told Politico, the goal is to ensure that the US isn’t too reliant on other countries and to make US-based supply chains more resilient. In his executive order calling for a review, Biden mentioned everything from another pandemic to a cyberattack to “climate shocks and extreme weather events” as examples of crises that could make it more difficult to get much-needed supplies in the future.
The supply chain review will be comprehensive. Over the course of the review — which is currently ongoing — the heads of several government agencies will reach out to industry stakeholders, researchers, NGOs, labor unions, and regional and local governments to study the supply chain. The Commerce Department, which is leading the semiconductor supply chain review, is soliciting public comment on all sorts of detailed questions about US chip manufacturing, from the location of chip manufacturing assets to the risks climate change could pose to chip production, as well as the risks faced if the US doesn’t boost its manufacturing capabilities in time.
In a few weeks, the Commerce Department is expected to submit to Biden its first report on the supply of semiconductor chips. Next year, it will submit an even broader report covering “critical sectors and subsectors of information and communications technology.”
“They’re going to be doing a thorough review of what are we able to do here: What are we already doing here versus what can we do here,” Ozkul, the supply chain expert, explained. That could be pretty difficult. Research firm McKinsey has noted that the average large company has more than 5,000 suppliers.
Even securing enough specialists to build a particular part of a device can be a challenge, as Willy Shih, a management practice professor, explained in Harvard Business Review last year. A typical laptop might require an LCD panel made by just a handful of billion-dollar facilities in Asia, as well as chips made by Intel that may be produced in the US but need to travel abroad for packaging. “The end result is that we have many suppliers scattered around the world upon whom manufacturers depend for critical components,” Shih explains, which makes it very hard for a manufacturer to be completely self-sufficient in a single country.
Following the supply chain review, the goal isn’t necessarily that the US produces all or even most of a particular product or its subcomponents, experts told Recode. Instead, it’s about making sure the country has stockpiles; coordinated supply chains of needed supplies and components from different parts of the world; and enough domestic manufacturing to ensure the US can weather another crisis.
But the task of building new high-tech manufacturing in the US would be a tall order. For instance, a 2017 deal then-President Donald Trump organized with the electronics giant Foxconn to build a massive LCD factory in Wisconsin — and create 13,000 jobs — turned out to be a dud. The billions of dollars in public investment for the Foxconn plant have resulted in just a fraction of the jobs originally promised and mostly empty buildings, though the company now says it might start building electric vehicles for Fisker there.
Meanwhile, provisions in the most recent National Defense Authorization Act have authorized the government to provide potentially billions in incentives for chip manufacturing in the US. Leaders of the chip industry are now urging Biden to fund these efforts, and members of Congress are considering next steps. Biden has said he’ll push for $37 billion for the effort. But boosting tech manufacturing in the US isn’t as simple as spending billions of dollars, canceling contracts around the world, ditching the global suppliers, and suddenly having a bunch of new jobs available to US workers.
“Before you blow up the old bridge, make sure you build a new bridge,” Tang said. “Make sure the new bridge is tested, and keep the old bridge running.”
Update, April 8, 2021, 5:55 pm ET: This piece has been updated to include new information about how the ongoing global chip shortage has impacted Apple and GM in April.
Open Sourced is made possible by Omidyar Network. All Open Sourced content is editorially independent and produced by our journalists.